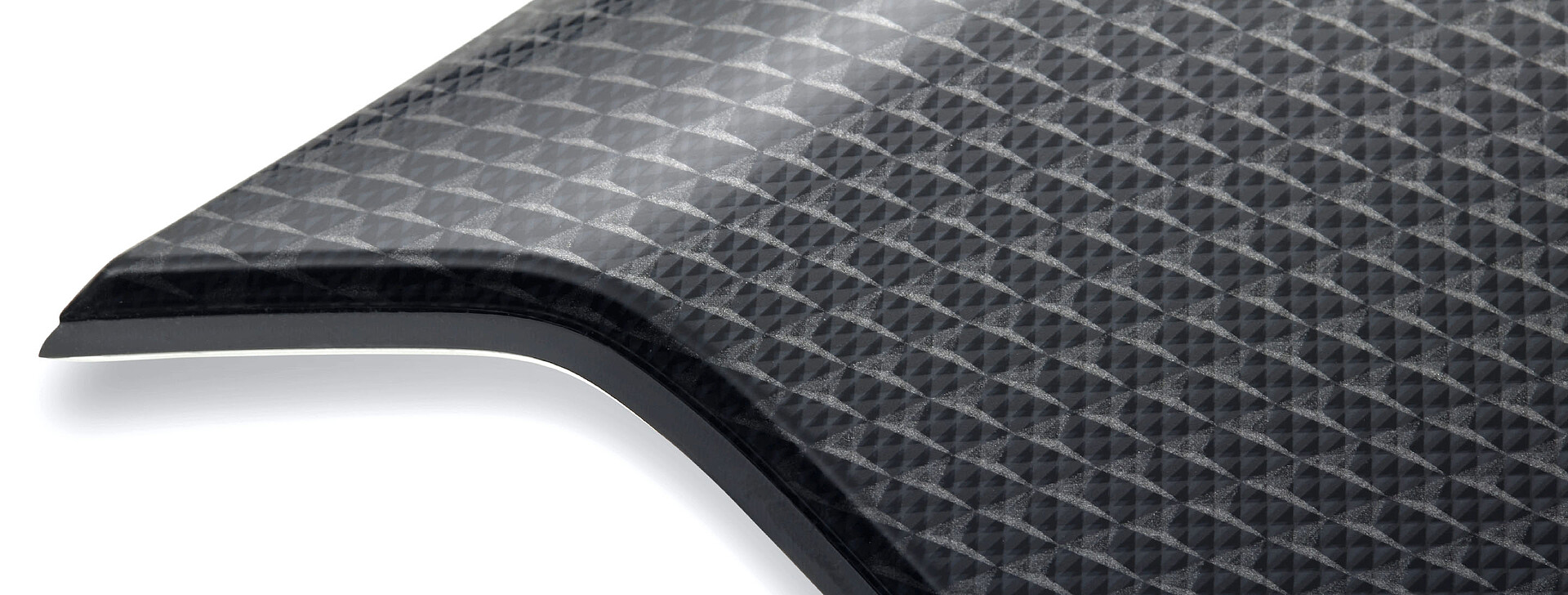
Insert molding
Efficient technology for complex geometries
This process enhances any interior. Insert molding can also be used to produce heavily shaped components that fit beautifully into the interior. And it’s extremely efficient: Hot Stamping, molding, and injection molding take place in a single process. There are no limits to the creativity of the designers. Backlighting and tactile designs are possible, as are haptic effects. Your benefit: Great freedom of design and movement as well as excellent cost efficiency.
- In the production cell, vacuum forming or compressed air forming and cutting of the individual component sheets takes place. The deformation temperature can be precisely metered for the respective raw material. The produced plastic part receives its preform and design. Then the still connected individual components on the belt are precisely separated.
- After cooling, high-precision punching takes place at another machine station. Here, openings and windows in the component can be removed in the same processing step. Such cutouts are needed to allow the addition of controls or a contrasting design at a later stage.
- The preformed and punched inserts continue on to the third finishing station for the final injection molding.
- This takes place in the closed machine chamber with reinforcing and stabilizing plastic. The results are decorated and precision-punched plastic components in their final shape, that can be easily integrated into end products.
Advantages
- Efficient processes that can be easily integrated into existing production lines
- Also works with recycled materials
- High degree of customization possible
- Possibility to implement designs that facilitate intuitive operation by the driver
- Adaptable to individual specifications
- Integration of PolyTC® sensors possible
- Shy tech design and backlighting possible